Predictive Maintenance: Establishing Predictive Maintenance at TRUMPF
Advantage
Reduction of downtime, increase of machine availability and optimization of service processes
Data
Sensor data of production machines
Tool
The empowerment approach of eoda in combination with YUNA - the dedicated platform solution for data-driven processes
TRUMPF is the world market and technology leader in the field of industrial lasers and laser systems. TRUMPF Laser Technology offers CO2 lasers, solid-state lasers, marking lasers and laser systems.
To keep performance and quality high as well as to avoid unforeseen machine breakdowns, predictive maintenance is to be enabled by means of data analysis, thereby increasing the quality and availability of machine performance.
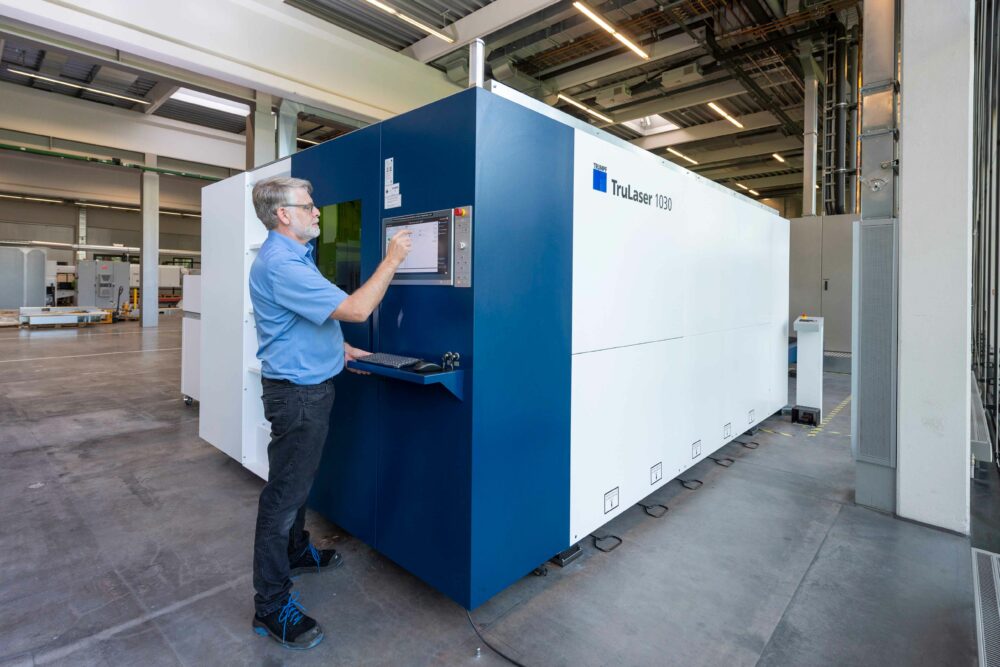
(Image source: TRUMPF / Martin Stollberg)
Aim
The implementation of the predictive maintenance approach and the fundamental increase of the digital maturity level based on data and algorithms: These two overarching goals were what drove TRUMPF before the project start with eoda.
- Adopt Data Science for exploratory use of data.
- Analysis of lasers whose sensors and system messages produce countless machine data daily
- Development of algorithms for pattern recognition of error patterns and prediction of future failures
- Transparent and descriptive visualization of machine data
- Introduction of cross-role and cross-departmental workflows to support business processes between development, service, after sales and external as well as internal data scientists
Solution
In the first step, eoda helped TRUMPF train its own data science team. The trained team thus combined domain knowledge and data expertise. This enabled it to quickly identify and successfully implement the first data science use cases. To perform the complex analyses of the machine data, TRUMPF relied on R, the leading data science programming language.
The realized use cases consisted of evaluating the existing machine data sets, analyzing them for anomalies and failures, and mapping the results and predicting future problems.
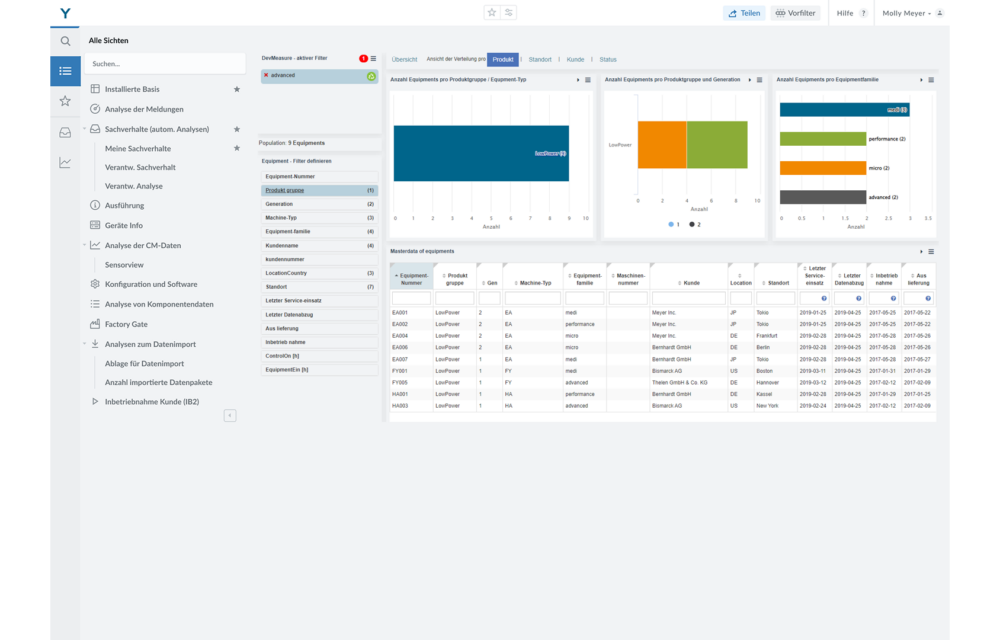
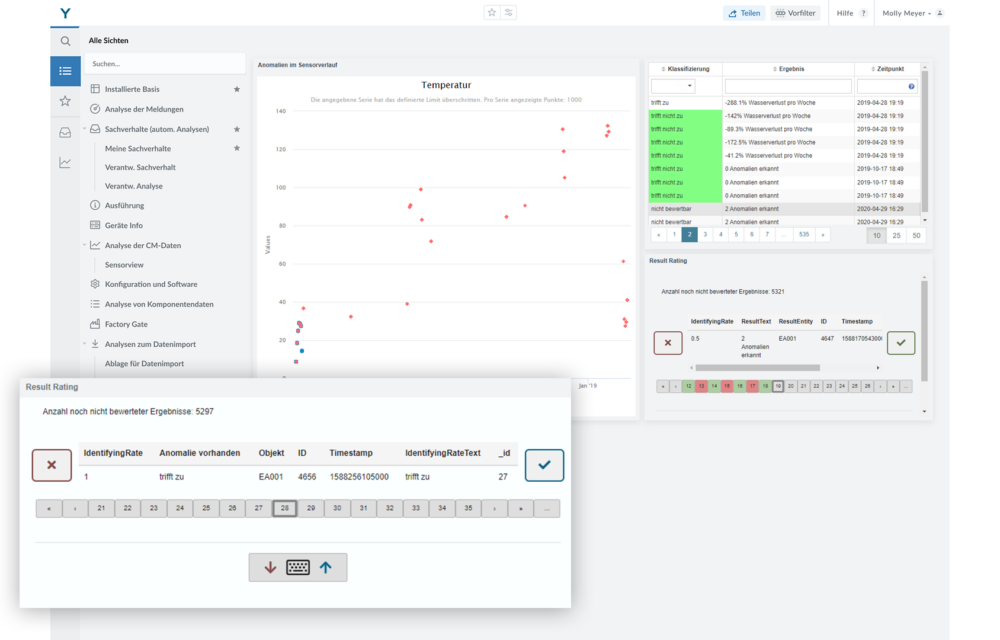
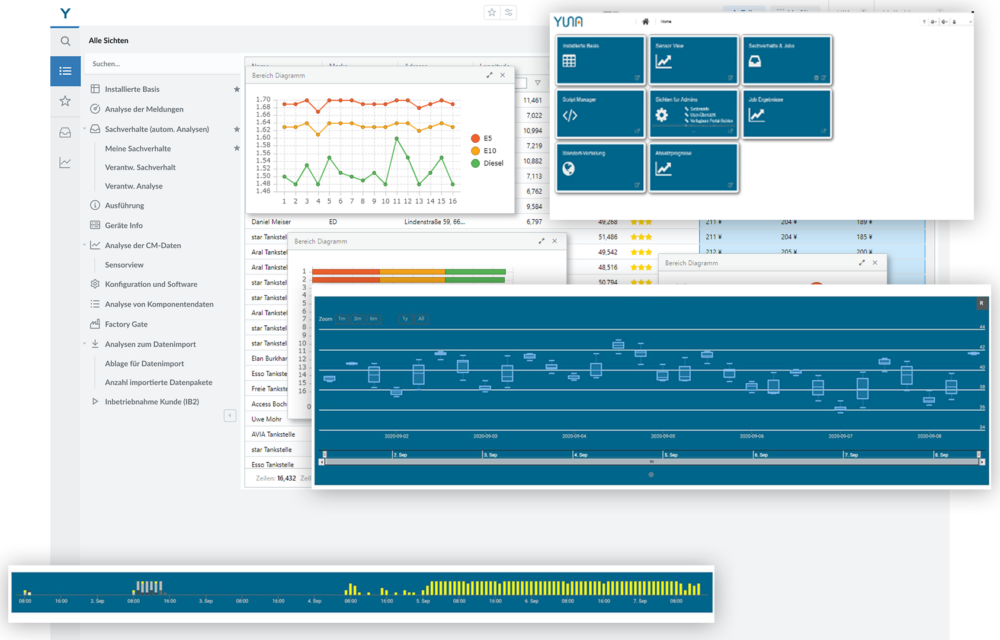
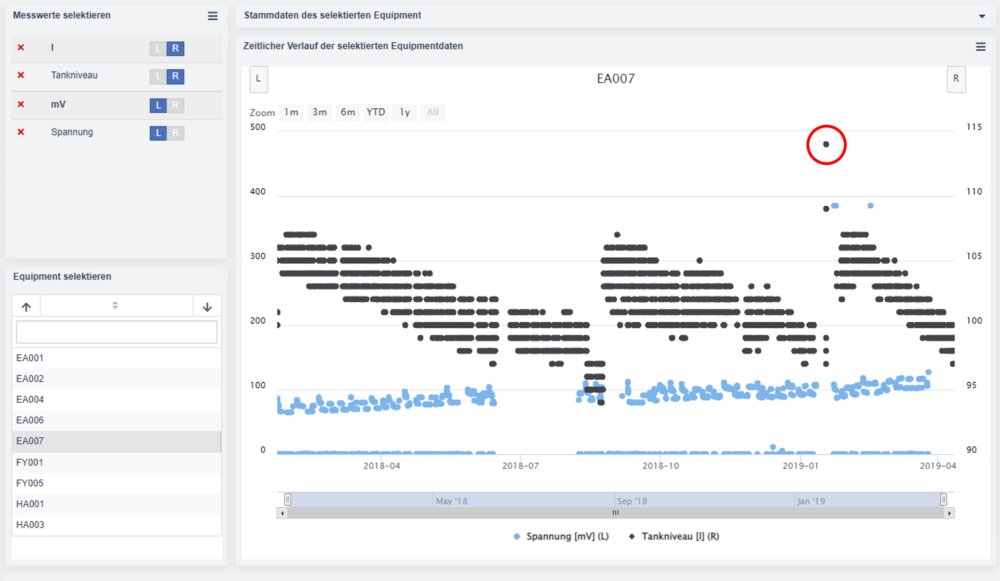
The departments involved and the management were sustainably convinced by the results of the analyses. In the further course, the focus was on the integration of data science into the existing business processes. For this purpose, a condition monitoring portal was developed on the basis of the eoda solution YUNA.
The condition monitoring portal makes it possible to monitor the condition of the machines and, in the context of predictive maintenance, to optimize the effort and costs of maintenance. The portal is an on-premise solution: TRUMPF retains complete control over the data and algorithms.
“YUNA by eoda enables us to fix problems before they actually occur. Thanks to real-time data evaluation, we reduce downtime, optimize processes and increase machine availability at the same time”.
Marco Holzer | Head of Product Management & Logistics Services | TRUMPF |
|
“YUNA by eoda enables us to fix problems before they actually occur. Thanks to real-time data evaluation, we reduce downtime, optimize processes and increase machine availability at the same time”.
Marco Holzer | Head of Product Management & Logistics Services | TRUMPF
Result
From the development of expertise to the productive use of the solution, eoda has accompanied TRUMPF and thus laid the foundation for data-driven business models.
As the centerpiece, the Condition Monitoring Portal brings the data, analyses and results into the daily business processes and thus sustainably increases the data centricity at TRUMPF. The information contained in the machine data becomes tangible – from development to service to after-sales. The Condition Monitoring Portal connects different departments, teams and roles through intuitive workflows, enabling collaborative work on data science use cases.
This makes it possible to create new data-based service, such as the realization of predictive maintenance. Through this, TRUMPF is able to detect machine malfunctions in advance and thus further increase the availability of its machines. The successful implementation of this use case is the impetus for many other digital initiatives at TRUMPF.
Successfully implement predictive maintenance and condition monitoring now