Advantage
Creation of new customer services based on data-based maintenance of the component and the associated increase in machine availability.
Data
Existing and unclassified data from rotary table control EF3.
Method
Anomaly detection: use of cluster/density-based methods to identify iO and niO states in the data.
With Condition Monitoring and Predictive Maintenance to the smart rotary indexing table for WEISS
Challenge
As a global system partner for factory automation, the WEISS Group designs automation solutions for the key industries of automotive, mechanical and plant engineering, life science and electronics at 17 locations and with around 500 employees. Central portfolio elements of WEISS are the leading rotary indexing and heavy-duty tables for efficient transport, movement and positioning of components in the production and assembly process.
The rotary tables are thus responsible for the transport and are usually installed in the lowest level of the machines. This makes the turntables a particularly critical machine component, whose maintenance is associated with great expense and machine downtime due to their location.
Goal
The rotary indexing and heavy-duty tables from WEISS have stood for reliability and quality for decades. In order to further expand these attributes, WEISS wants to obtain reliable information about the machine condition and predict disruptions with predictive maintenance. This should further increase the reliability of the rotary tables for customers and ensure the most maintenance-free operation possible.
Solution
To achieve this vision, WEISS has defined three milestones:
- Condition monitoring: Establishment of continuous condition monitoring
- Anomaly detection: Detection of critical conditions based on the transmitted data
- Predictive Maintenance: Prediction of disruptions and proactive intervention
Together with the data science experts from eoda, WEISS defined concrete value propositions in a workshop based on different customer journeys, which are to be created with the IoT features to be developed:
- Service Management: Through local machine monitoring, the service manager can be proactively informed about anomalies at the plant and receive automated solution suggestions.
- Plant Management: As part of the service contract, WEISS monitors the installed components at the customer’s site, delivers informative reports to the customer and proactively triggers necessary maintenance measures.
- Data Science: Through the data interface via OPC-UA, the data scientists at the customer’s site can directly access the data of the WEISS components, link it with their other data and easily integrate it into their own processes and analyses.
In the first development step, eoda supported WEISS in building an architecture for the implementation of the data solution. This architecture structure ranges from the OPC-UA interface to the sending of push messages of the machine status to the customers and is thus the basic technical framework for the development of Smart Services.
After this, eoda completed the data management and anomaly detection analysis development. Through the use of cluster / density based techniques, known iO and niO states were identified in the data. Data patterns that do not correspond to any of the known states are labeled as an anomaly. The information basis was the existing unclassified data from the EF3 rotary table control.
In order to be able to optimally display and use the relevant machine data and analysis results internally at WEISS, eoda also took on the development of the dashboards. The dashboards enable the technical experts at WEISS to easily and quickly record the condition of the components and, if necessary, directly initiate maintenance at the customer’s site. The dashboards developed are based on eoda’s own established data science platform YUNA, which is also used, for example, by the machine manufacturer TRUMPF as a Condition Monitoring Portal.
Result
With the support of eoda, WEISS can generate a number of added values for both machine builders and machine operators. The rotary and heavy-duty tables become smart machine components through the Condition Monitoring and Predictive Maintenance modules, which actively report changes in condition and thus further reduce the risk of long, unplanned downtimes. For WEISS itself, this creates the opportunity to offer proactive machine monitoring as a digital service for its customers.
Consulting, project services and software development: With eoda, WEISS received all the necessary development steps for this project from a single source. By using the proven and flexibly adaptable YUNA components, WEISS has saved valuable development time and costs.
Data-Driven Software:
YUNA – Data Science Platform
YUNA is the central platform for the development and control of digital, AI-supported projects. It combines BI functions with the possibility to use various models and scripts.
Learn more!
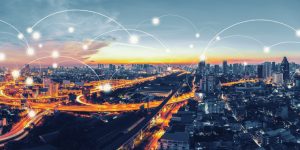
Use Cases:
Data Science in your industry
Optimized processes, time savings and cost reductions - these are the results when Data Science is used successfully. Discover more use cases here and get inspired.
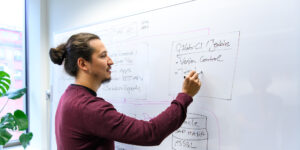
Data Science Infrastructure:
On Premise, Cloud or Hybrid
Design, implementation and support! We are the provider of resilient and reliable data-driven services. We also make your infrastructure ready for the digital challenges of the future!
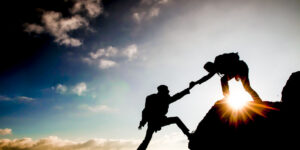
Data Projects:
From the idea to productive service!
Which use cases are particularly purposeful for you? How can knowledge creation succeed in your company? From the solution idea to the productive use of AI systems in your company: We create perceptible added value for you from data.